铁矿石烧结是挥发性有机化合物(VOCs)的产生源之一。目前中国钢铁工业烧结过程VOCs排放基本处于“无标准、无监测、无检测”的阶段,对VOCs排放量尚不清楚。总结了国内外钢铁工业烧结过程VOCs排放现状及标准,分析了烧结过程VOCs的生成机理。结果表明,VOCs主要由焦炭、含油氧化铁皮等原燃料中的挥发性物质形成,并以气体形式排放。将VOCs减排方法分为源头削减、过程控制及末端治理3种。源头削减是减少粉尘和轧屑的油类带入,是烧结过程抑制VOCs产生的最佳选择;过程控制是将烧结台车的部分热废气再次引入烧结料层循环利用,热废气所含的VOCs在通过1300℃以上的烧结带时被分解;末端治理主要有活性炭法和MEROS法。上述技术在中国部分钢铁企业都有应用实践。随着VOCs标准的制定,中国钢铁工业烧结过程VOCs有望在现有技术基础上达标排放。
1中国对VOCs的管控政策
2010年,中国环境保护部、发改委和科技部等部门联合制定了《关于推进大气污染联防联控工作改善区域空气质量的指导意见》,首次将开展VOCs防治工作列为大气污染联防联控的重要组成部分。2012年底,中国环境保护部、财政部和发改委联合发布的《重点区域大气污染防治“十二五”规划》提出,现有挥发性有机物(VOCs)污染控制力度已难以满足人民群众对改善空气质量的迫切要求,从VOCs排放控制角度提出严格环境准入、开展重点行业治理、完善VOCs污染防治体系的要求,标志着国家正式提出VOCs的防治目标,即在2015年全面展开VOCs防治工作。
2013年5月,中国环境保护部发布了《挥发性有机物(VOCs)污染防治技术政策》,提出了生产VOCs物料和含VOCs产品的生产、储存运输销售、使用、消费各环节的污染防治策略和方法,提出VOCs污染防治应遵循源头和过程控制与末端治理相结合的综合防治原则。要求在2015年,基本建立起重点区域VOCs污染防治体系;到2020年,基本实现VOCs从原料到产品、从生产到消费的全过程减排。文件囊括了石油炼制与石油化工、煤炭加工与转化等含VOCs原料的生产行业,油类(燃油、溶剂等)储存、运输和销售过程,涂料、油墨、胶粘剂、农药等以VOCs为原料的生产行业,涂装、印刷、黏合、工业清洗等含VOCs产品使用过程的污染防治。
2014年中国环境保护部发布《石化行业挥发性有机物综合整治方案》,提出在2017年全国石化行业VOCs排放总量比2014年削减30%以上的目标。2015年中国财政部、发改委和环境保护部等部门发布了《挥发性有机物排污收费试点办法》,通过征收排污费驱动重点行业VOCs减排工作。可见,自2012年以来,国家对大气治理行业逐步重视,大气治理的重心由除尘、脱硫、脱硝向VOCs治理方向倾斜。近年来颁布的关于VOCs治理的政策法规,极大地加快了VOCs治理行业的发展。
2钢铁工业烧结过程VOCs的生成机制及减排技术
2.1钢铁工业烧结过程VOCs的生成机制分析
一般认为VOCs主要来源于燃煤。由于烧结过程使用燃料,因而不可避免地会产生VOCs。烧结过程中,VOCs是由焦炭、含油氧化铁皮等中的挥发性物质形成的,以气体形式排放,在某些操作条件下同时形成二英和呋喃。烧结预热带温度范围基本为100~900℃,厚度大约为100~200mm,持续时间为10min左右。随烧结进行,燃料颗粒温度升高,内部有机挥发物呈气态挥发到气流中,随气流向下运动,下部温度较低,含有机挥发物的气流热交换后温度降低,其中有机挥发物根据沸点高低逐步冷凝(图1)。由于冷凝速度较快,形成许多微小颗粒,这也是粉尘形成的原因之一。
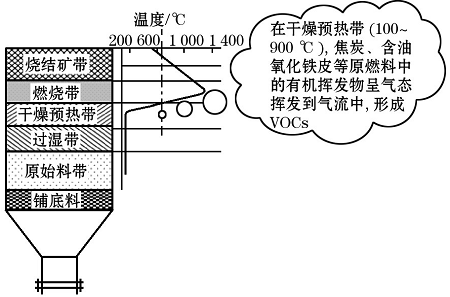
图1 VOCs在烧结过程中生成机理
2.2钢铁工业烧结过程VOCs的减排技术
国内外钢铁工业在减少烧结过程VOCs排放方面采取的措施可分为源头削减、过程控制和末端治理3类。
2.2.1源头削减
由于大部分石油碳氢化合物在温度为100~800℃时在烧结混合物中挥发,并且通过废气从烧结过程排出,因此,减少含油粉尘和轧屑的使用可减少VOCs排放,主要技术包括:分开挑选低含油量的粉尘和轧屑以限制油类投入;减少轧屑的含油量;净化轧屑,加热轧屑至800℃,使石油碳氢化合物挥发;使用溶剂从轧屑中提取油类。
2.2.2过程控制
采用烧结烟气循环工艺将烧结台车的部分热废气(即烧结机头烟气)再次引入烧结料层循环利用,热废气所含的VOCs在通过1300℃以上的烧结带时被分解。目前,国内外钢铁企业已工业化的典型烧结烟气循环工艺主要有日本新日铁开发的区域性废气循环技术、荷兰艾默伊登开发的EOS、德国HKM开发的LEEP以及奥钢联公司开发的EPOSINT。中国对烧结烟气循环工艺的研究和应用刚刚起步,宁波钢铁公司于2013年采用了烧结烟气循环技术。
2.2.3末端治理
在末端治理方面,主要有日本的活性炭法、林茨钢厂和奥钢联的MEROS法。
(1)活性炭法。活性炭法是烧结烟气经旋风除尘器简单除尘后,粉尘浓度从1000降为250mg/m3,由主风机排出。烟气经升压鼓风机后送往移动床吸收塔,并在吸收塔入口处添加脱硝所需的氨气。
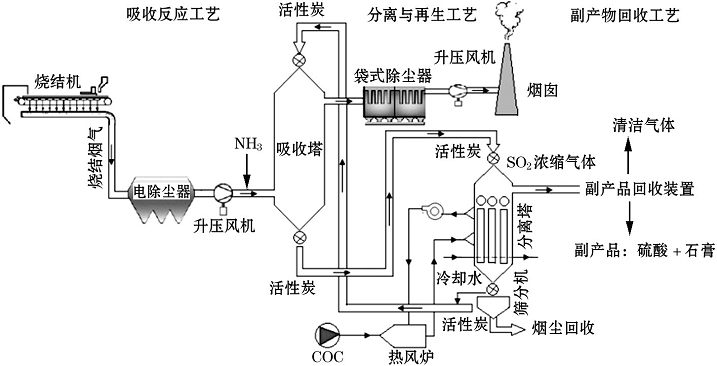
图2 活性炭法脱硫工艺流程
烟气中的SO2、NO在吸收塔内进行反应,生成硫酸和铵盐被活性炭吸附除去。吸附了硫酸和铵盐的活性炭送入脱离塔,经加热至400℃左右即可解吸出高浓度SO2。解吸出的高浓度SO2可以用来生产高纯度硫黄(99.95%以上)或浓硫酸(98%以上),再生后的活性炭经筛分机除杂质后送回吸收塔进行循环使用(图2)。活性炭法主要靠活性炭表面孔隙吸附VOCs。国外较多企业采用活性炭法(表1),国内太钢等钢铁企业也使用活性炭法。
表1 国外钢铁工业主要的烧结烟气净化装置的设置情况
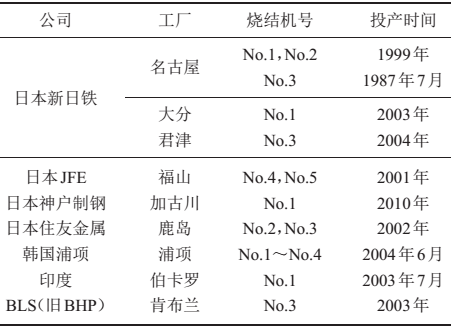
(2)MEROS法。MEROS法是将添加剂均匀、高速并逆流喷射到烧结烟气中,然后利用调节反应器中的高效双流(水/压缩空气)喷嘴加湿冷却烧结烟气。如图3所示,离开调节反应器之后,含尘烟气通过袋式过滤器去除烟气中的粉尘颗粒。为了提高气体净化效率和降低添加剂费用,袋式除尘器中的大多数分离粉尘循环到调节反应器之后的气流中。其中部分粉尘离开系统,输送到中间存储筒仓。MEROS法集脱硫、脱HCl和HF于一身,并可以使VOCs可冷凝部分几乎全部去除。目前国内马钢采用MEROS工艺。
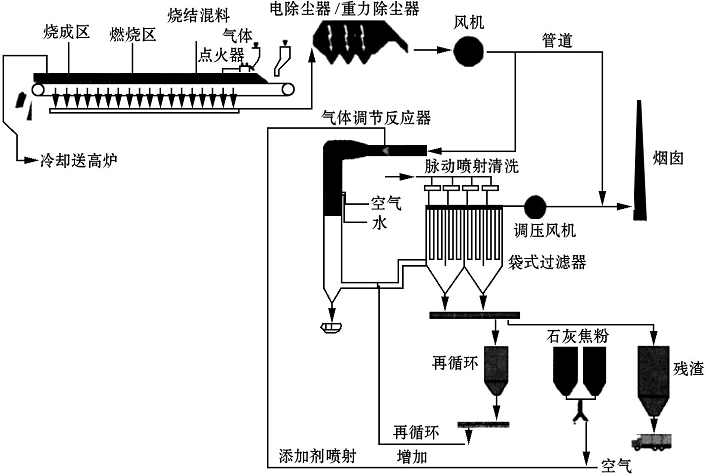
图3 MEROS法脱硫工艺流程
3 结语
国外先进产钢国家对烧结烟气VOCs排放的控制较为严格,治理取得了较好效果,但相关技术和管理的详细报道较少。由于缺乏标准和系统监测,国内绝大部分钢铁工业烧结过程VOCs排放尚不清楚。未来,中国应借鉴发达国家经验,尽快制定VOCs排放清单及行业标准,以明确企业的VOCs排放类型及排放量,从源头减少VOCs的产生。同时,结合现有烟气循环技术和末端治理技术,达到协同减少VOCs排放的目的。